Innowacyjne systemy kotwienia
KOTWA-PRO
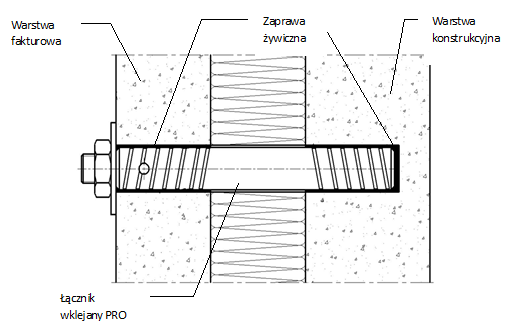
Oferujemy najlepszy system kotwienia na rynku pod względem ceny, nośności oraz prostoty montażu.
Kotwienie odbywa się przy pomocy 2 łączników na płytę niezależnie od liczby starych wieszaków i długości płyty.
Łączniki wklejane Kotwa-PRO składają się z trzpienia o średnicy 23 mm wykonanego ze stali nierdzewnej. Łącznik wykonywany jest z pręta ze stali nierdzewnej nagwintowanego z jednej strony, z nawierconym otworem wzdłuż osi pręta oraz przecinającymi go otworami poprzecznymi, które służą do wprowadzania zaprawy żywicznej. Nagwintowana część umożliwia regulację zagłębienia łącznika w ścian warstwowych budynków wielkopłytowych.
Otwory w kotwie zapewniają stabilne i trwałe osadzenie kotwy w płycie po zaschnięciu zaprawy żywicznej. Do nagwintowanej części kotwy przykręcane są podkładka i nakrętka. Kotwa na obu końcach jest wyposażona spiralne w rowki, które umożliwiają skuteczne rozprowadzenie oraz wnikanie zaprawy żywicznej.
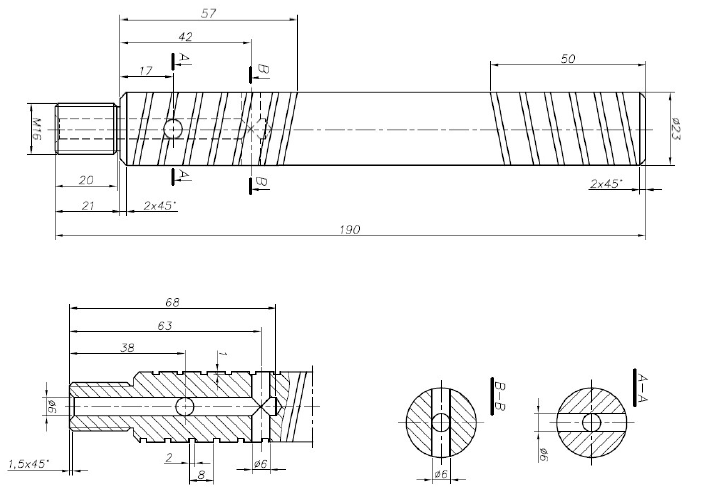
PREZENTACJA – INSTRUKCJA MONTAŻU
RM KOTWA KOMPOZYTOWA
W ramach bonu innowacyjnego został przebadany prototyp w postaci RM KOTWA KOMPOZYTOWA
Prototypowy dyblo-kotwo-łącznik zwany dalej kotwą kompozytową RM składa się z trzech głównych elementów: pręta kompozytowego, kołka rozporowego i talerzyka. Te trzy elementy o łącznej długości dostosowanej do grubości konstrukcji i grubości nowej izolacji, stanowią integralny element kotwy kompozytowej RM.
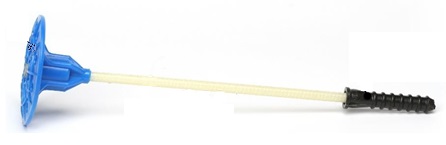
Pręt kompozytowy o długości od 200 do 350mm, w zależności od wymaganej długości kotwy wykonany został z włókna szklanego (nieprzewodzący ciepła i odporny chemicznie), o średnicy 6,0mm. Pręt na jednym końcu został lekko zaostrzony umożliwiając bezproblemowe wejście pręta w kołek rozporowy, na drugim końcu posiada on pogrubienie będące wzmocnieniem miejsca uderzenia młotkiem oraz pełniącym funkcję klina w gnieździe talerzyka
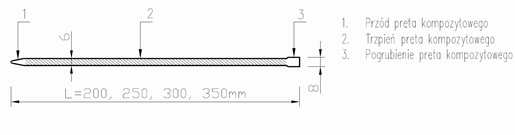
Kołek rozporowy jako element kotwiący wykonany jest z poliamidu o długości 50 mm, 80 mm lub 100 mm, w zależności od materiału z którego jest wykonana ściana izolowana.
Talerzyk dociskowy o średnicy 60 mm, znajdujący się na końcu pręta, gdzie występuje pogrubienie przekroju. Gniazdo talerzyka o długości 35 mm.
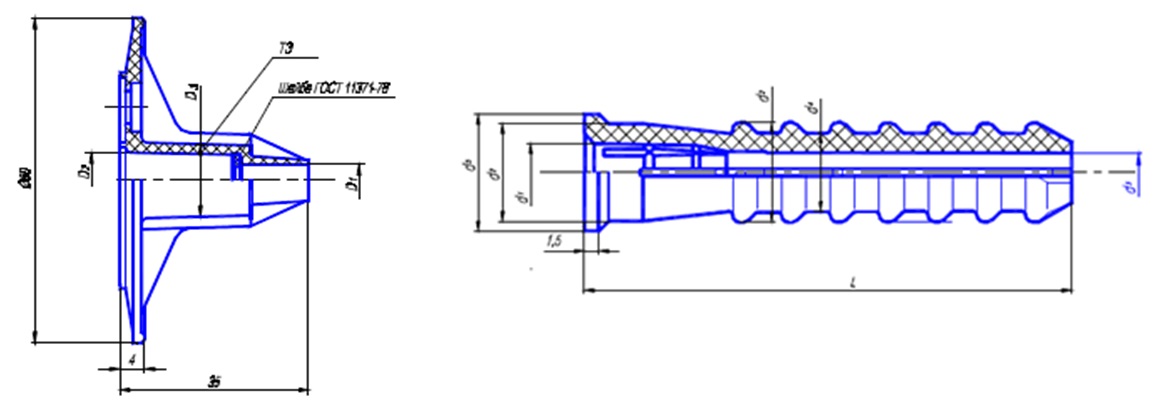
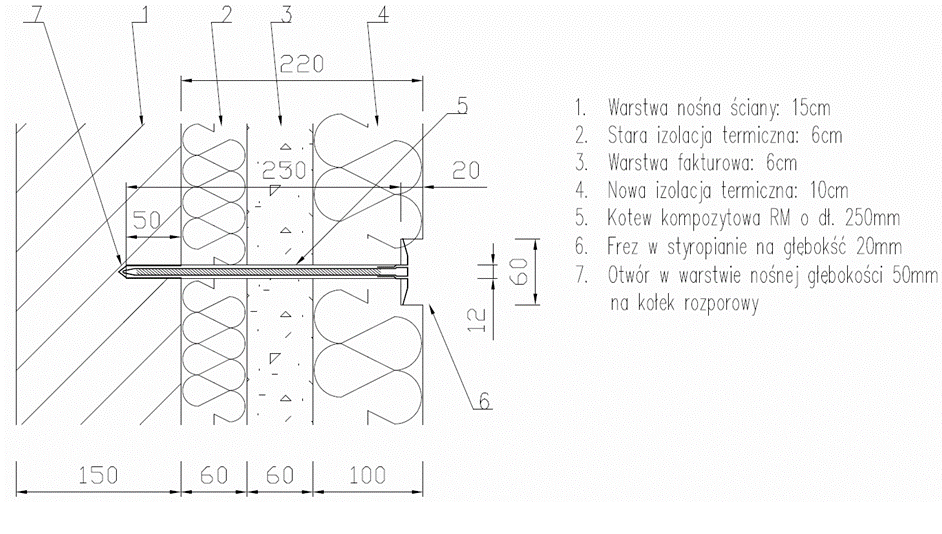
Zastosowanie prototypowego systemu dyblo-kotwo-łączników zwanych kotwami kompozytowymi RM eliminuje dwuetapowość procesu termomodernizacji budynków wykonanych z wielkiej płyty. Ujednolica proces prowadzenia pracy termomodernizacyjnych. W jednym cyklu pracy wzmacniamy warstwę fakturową oraz dyblujemy warstwę izolacyjną. Dodatkowo dostajemy niemalże powierzchniowe połączenie warstwy fakturowej z częścią nośną ściany, uzyskując efekt przeszycia.
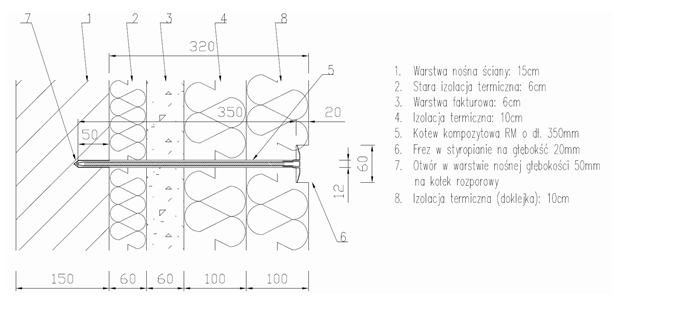
PROCES MONTAŻU
Proces montażu kotwy kompozytowej RM, jest procesem stosunkowo prostym. Składa się z kilku podstawowych kroków:
Krok 1: Wykonanie procesu termoizolacyjnego polegającego na wyklejeniu płyty warstwowej styropianem. Rozplanowanie otworów pod montaż kotew.
Krok 2: Wykonanie otworów jedynie w nowej warstwie izolacyjnej oraz warstwie fakturowej i starej izolacji termicznej. W tym celu należy używać wierteł diamentowych o średnicy 12mm. Najlepiej z funkcją do wiercenia w betonie zbrojonym.
Krok 3: Wykonanie pomiaru, za pomocą nawigatora (pręta stalowego o fi równym 10mm), rzeczywistej grubości trzech przewierconych warstw: starej izolacji termicznej, warstwy fakturowej oraz nowej izolacji termicznej.
Krok 4: Określenie potrzebnej długości kotwy kompozytowej RM. Pomiar rzeczywistej grubości z kroku nr 3 powiększony o 3 cm.
Krok 5: Wykonanie otworu w warstwie konstrukcyjnej ściany na głębokość 5cm. Oczyszczenie otworu z zanieczyszczeń za pomocą sprężonego powietrza. Potwierdzenie całkowitej głębokości montażowej za pomocą nawigatora.
Krok 6: Wykonanie frezu o głębokości 2cm w nowej warstwie izolacji termicznej. Wprowadzenie kotwy kompozytowej RM do otworu. Uderzając młotkiem w trzpień pręta kompozytowego dokonać kotwienia warstwy izolacyjnej z jednoczesnym wzmocnieniem warstwy fakturowej ściany warstwowej.
Powyższy syntetyczny opis procesu montażu kotew kompozytowych RM można uszczegółowić rozwijając każdy z przytoczonych sześciu punktów. I tak:
Krok 1 i 2: Po wykonaniu procesu termoizolacyjnego polegającego na wyklejeniu płyty warstwowej styropianem należy rozplanować i przygotować otwory pod montaż kotwy. Otwory należy wykonać jedynie w nowej warstwie izolacyjnej, warstwie fakturowej oraz starej warstwie izolacji termicznej. Do tego celu najlepiej jest użyć wiertła diamentowego o średnicy fi 12mm. Zaleca się używanie wierteł z funkcją do wiercenia w betonie zbrojonym. Poniżej przedstawiono proponowany rozkład kotew kompozytowych RM w procesie termomodernizacji. Ilość i schemat rozmieszczenia kotew kompozytowych RM zależeć będzie od konieczności uzyskania odpowiedniego poziomu nośności dyblo-kotwo-łącznika, który w głównej mierze ma za zadanie wzmocnić wielowarstwową ścianę systemu „Wielkiej Płyty”
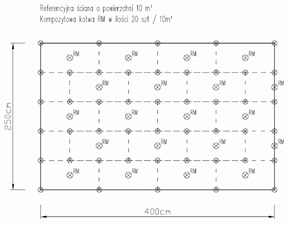
Schemat rozmieszczenia kotw kompozytowych RM
Krok 3 i 4: Następny krok polega na zmierzeniu za pomocą nawigatora (pręta stalowego o średnicy fi 10mm) rzeczywistej grubości trzech przewierconych warstw: starej izolacji termicznej, warstwy fakturowej oraz nowej izolacji termicznej (np. 6 cm stara izolacja + 6 cm warstwa fakturowa + nowa izolacja termiczna ze styropiany grubości np. 10 cm). Do otrzymanego wyniku dodajemy 3 cm (głębokość otworu w warstwie nośnej 5cm odjąć 2 cm głębokości frezu). Co daje nam: 22cm + 3cm = 25cm . Jest to docelowa długość pręta kompozytowego.
Ponadto dzięki dokonanym pomiarom dokonujemy doboru docelowej długości pręta kompozytowego w systemie kotwy kompozytowej RM, tj.:
1. 25cm szpilka – gdy nowa izolacja wynosi 10 cm
2. 30cm szpilka – gdy nowa izolacja wynosi 15 cm
3. 35 cm szpilka – gdy nowa izolacja wynosi 20 cm
Przy prawidłowym dobrze długości sprawiamy że frez wykonywany w styropianie zawsze będzie wynosił 2cm głęboki.
Krok 5 i 6: Krok ten obejmuje wykonanie otworu o głębokości 5 cm w warstwie konstrukcyjnej na kołek rozporowy o średnicy fi 10 mm. Po wykonaniu otworu, otwór ten należy oczyścić z luźnych i wolnych elementów powstałych podczas wiercenia. Do tego celu zaleca się zastosować bezprzewodową sprężarkę akumulatorową. Po oczyszczeniu otworu należy wykonać ponowny pomiar, za pomocą nawigatora, potwierdzający wcześniej określona całkowita długość zestawu kotwy kompozytowej RM. Następnie w nowej warstwie izolacji termicznej wykonuje się frez pod talerzyk dociskowy o głębokości 2cm. Wprowadza się kotew kompozytową RM do otworu i uderzając młotkiem w trzpień pręta kompozytowego dokonuje się kotwienia warstwy izolacyjnej z jednoczesnym wzmocnieniem warstwy fakturowej ściany warstwowej. W procesie tym zaostrzony element kotwy kompozytowej znajdujący się w kołku rozporowym w wyniku uderzenia w pogrubioną część kotwy, ulega zagłębieniu w kołek rozporowy, natomiast pogrubiona część znajdująca się na wysokości talerzyka ulega zagłębieniu w nieprzelotowym gnieździe talerzyka dociskowego.
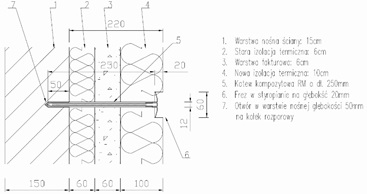
Montaż kotwy kompozytowej RM w warstwie nośnej ściany wielowarstwowej
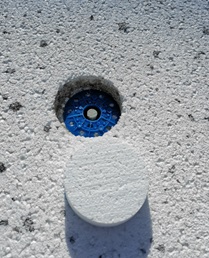
Wykonany frez na talerzyk
Dzięki elastyczności systemowej opartej na z unifikowanym doborze długości pręta kompozytowego do grubości nowopowstającej izolacji termicznej powinniśmy standardowo otrzymywać również zunifikowaną głębokość frezu pod talerzyk dociskowy, wynoszącą 2 cm. Głębokość ta odpowiada grubości stosowanym najczęściej i powszechnie dostępnym dekielkom styropianowym, które służą jako „zatyczki” otworów powstałych po frezowaniu. Doskonale to pokazuje uniwersalność opracowanego systemu kotew kompozytowych RM z obecnymi już na rynku rozwiązaniami technicznymi.
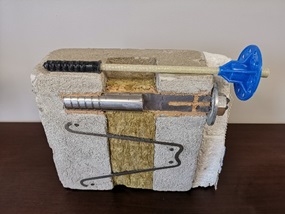
Przedstawienie stosowanych systemów
RM KOTWA CHEMICZNA
Innowacyjny system łączników kompozytowych do kotwienia i łączenia różnego rodzaju materiałów budowlanych z wykorzystaniem chemii i prętów GFRP
Wytworzony w ramach bonu prototyp dotyczy łącznika/kotwy przeznaczonej do spajania ze sobą materiałów różnego typu. Ponadto łączniki znajdą zastosowanie w szczególnie trudnych warunkach, ze względu na odporność zastosowanych materiałów na środowiska agresywne.
Spaja np. materiały budowlane takie jak: cegła, beton, gazobeton z metalem, drewnem itd. Funkcja taka może być zastosowana do wykonania różnego rodzaju systemów wsporczych, montażowych lub innych zastosowań związanych z techniką zamocowań.

BUDOWA:
1. Trzpienia w postaci prętów GFRP o średnicach od 4 mm do 40 mm.
2. Elementu mocująco – dociskowego w postaci nakrętki dostosowanej do średnicy i uzwojenia pręta wykonanej techniką druku 3D (na potrzeby prototypowania) z filamentu PETG,
3. Elementu kotwiącego trzpień łącznika w podłożu czyli kotwy chemicznej w postaci żywicy dwuskładnikowej winyloestrowej bez styrenu.
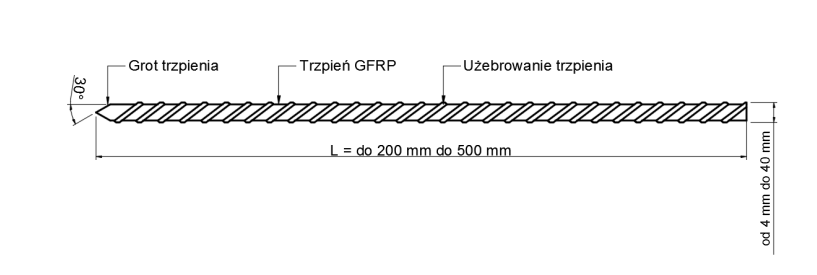

Parametry wytrzymałości kotwy chemicznej są najwyższe ze wszystkich znanych łączników. Chodzi zarówno o wielotonowy udźwig obciążeń, jak i wytrzymałość na obciążenia pulsacyjne. Kotwa chemiczna wypełnia szczelnie wszelkie nierówności, zagłębienia i zarysowania istniejące między łączonymi materiałami, a następnie zastyga i zostawia bardzo trwałe połączenie.
Kotwy chemiczne dają także spory komfort przy mocowaniu elementów wymagających odpowiedniego usytuowania. W żywicę tworzącą kotwę chemiczną, możemy wklejać elementy o bardzo różnej powierzchni czy wielkości.
Zastosowany pręt GFRP jest wielokrotnie bardziej wytrzymały na obciążenia mechaniczne niż stal.
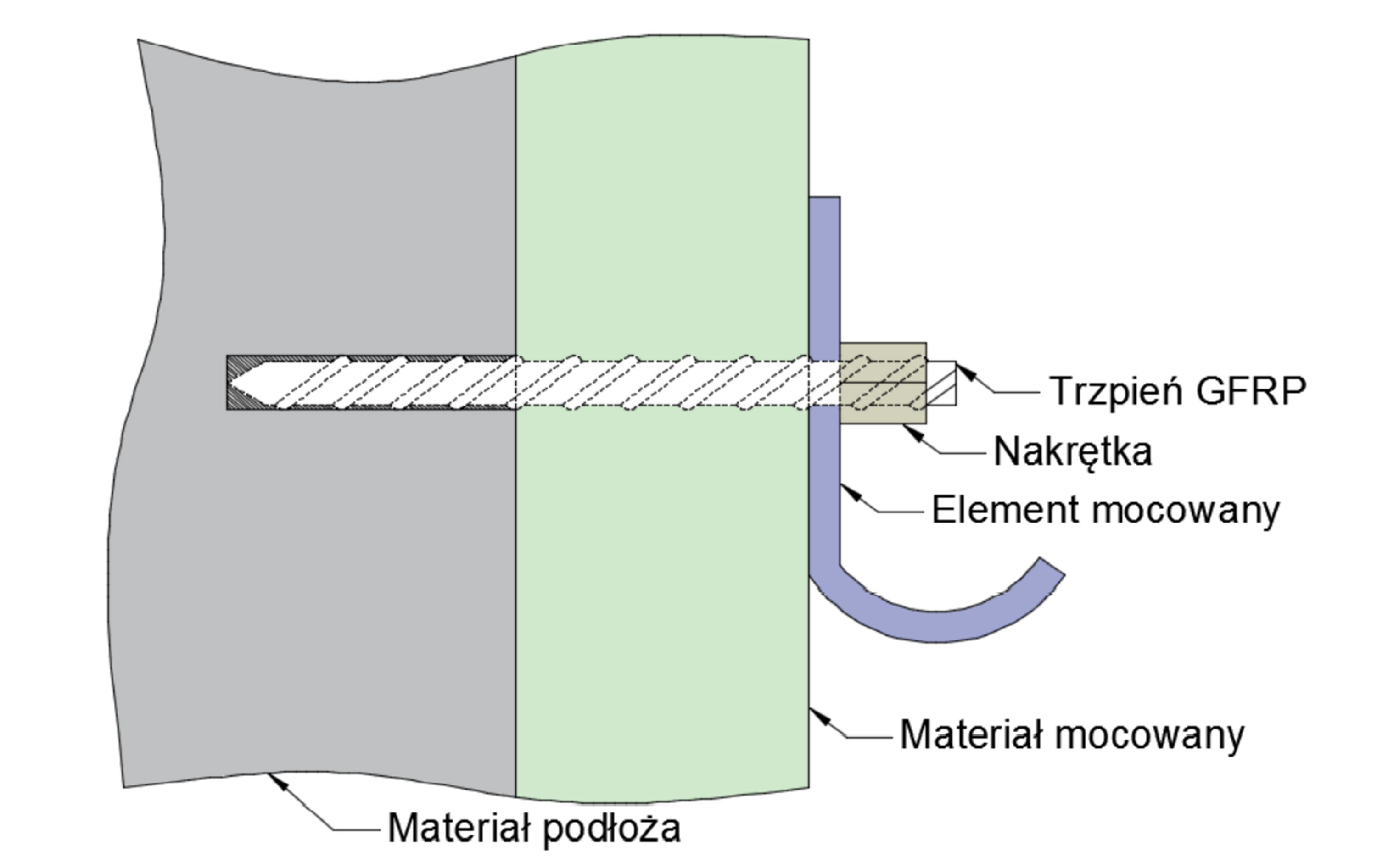
Najważniejszą właściwością prętów GFRP jest ich odporność na agresywne środowiska (korozja). Pręt ten może być używany wszędzie tam, gdzie nie jest możliwe użycie stali jako łącznika ze względu na szybko zachodzący proces korozji. Bardzo ważna jest również łatwość cięcia takiego pręta na pożądana długość.
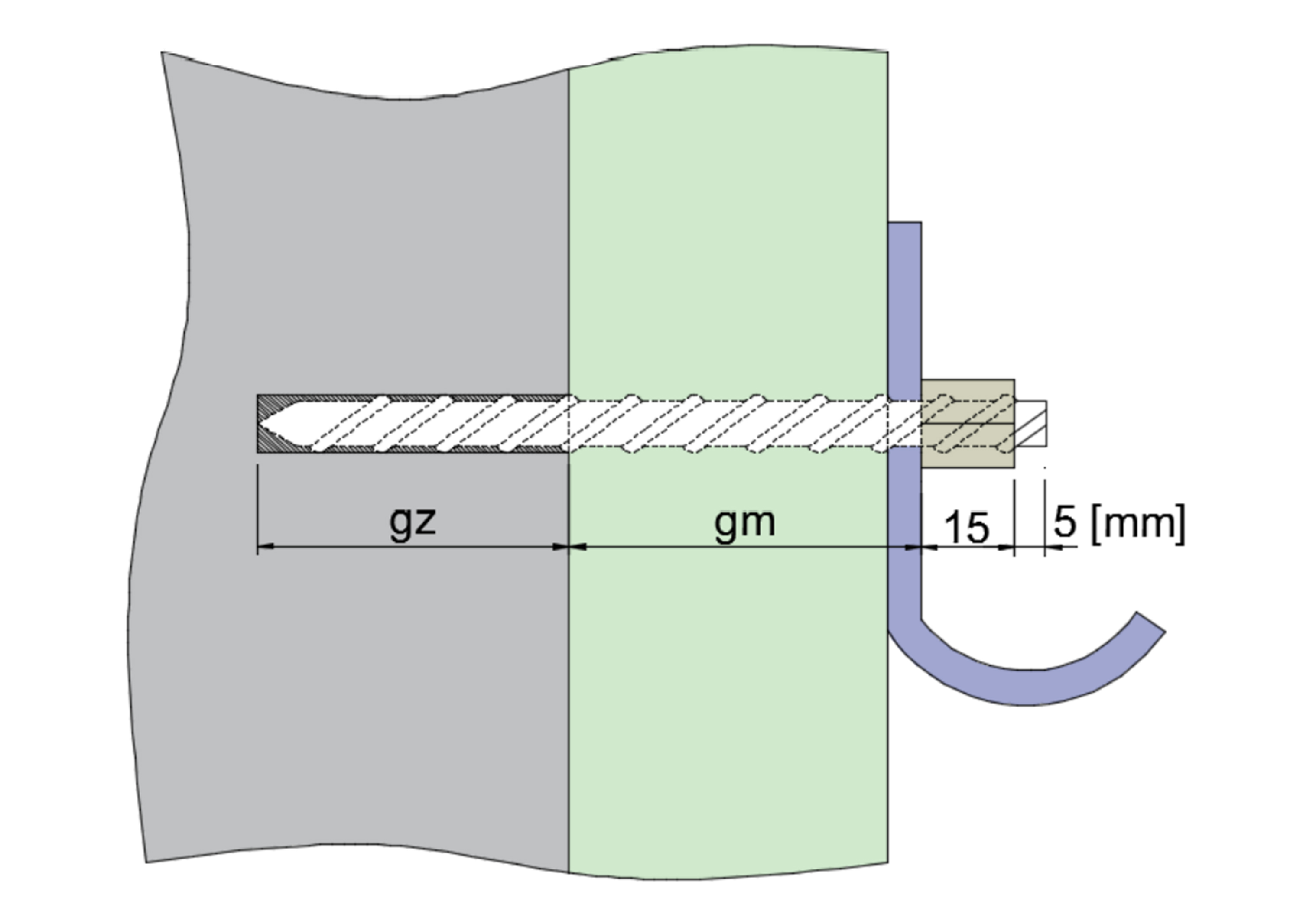
Do mocowania trzpienia łącznika GFRP RM w podłożu zastosowano kotwę chemiczną w postaci żywicy winyloestrowej bez styrenu.
PARAMETRY ŁĄCZNIKÓW
KOTWA-PRO
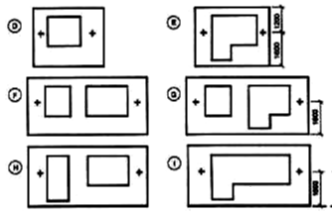
- jedyny na rynku łącznik o nośności obliczeniowej >18 KN
- wysokostopowa stal nierdzewna
- system zgodny z instrukcją ITB360/99
- przeznaczony dla betonów klas >c12/15
- szybki, prosty i bezudarowy system montażu
- długość łącznika dostosowana do typu ścian
- niezależnie od wymiarów płyty – zawsze stosujemy dwa łączniki
RM KOTWA KOMPOZYTOWA
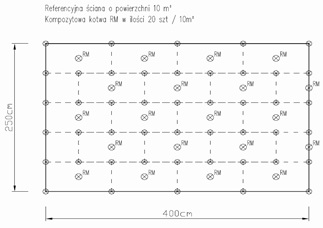
Dzisiejsze rozwiązanie RM Kotwa Kompozytowa została przebadana w laboratorium Instytutu Budownictwa Uniwersytetu Zielonogórskiego:
Dzięki otrzymanym wynikom i właściwościom cechującym RM Kotwa Kompozytowa otrzymaliśmy system, który pozwalana nam wykonywanie izolacji termicznej, dyblowania i wzmacniania jednocześnie.
Do mocowania trzpienia łącznika GFRP RM w podłożu zastosowano kotwę chemiczną w postaci żywicy winyloestrowej bez styrenu.
PODSUMOWANIE BADAŃ I ZAŁOŻEŃ
System Kotwy Kompozytowej RM – podsumowanie założeń i badań wytrzymałościowych
Przyjęta na samym początku idea mająca na celu stworzenie systemu, który w jednym procesie wzmacnia warstwę fakturową ściany wielowarstwowej systemu W-70 lub pokrewnego oraz dybluje styropian, stanowiący nową warstwę izolacji termicznej budynku, wymagała przeprowadzenia badań wytrzymałościowych. Badania te przeprowadzone zostały w laboratorium Instytutu Budownictwa Uniwersytetu Zielonogórskiego na sześciu próbkach o wymiarach 50x50cm. Próbki te pochodziły z rzeczywistej płyty warstwowej systemu W-70 pozyskanej na cele badań, która to dodatkowo została ocieplona warstwą styropianu grubości 10cm.
System Kotwy Kompozytowej RM z założenia jest dość elastyczny. Pozwala bowiem projektantowi opracowującemu projekt termomodernizacji obiektu na dostosowanie ilości potrzebnych kotew RM oraz ich średnicy w zależności od obciążenia jakie mają one przenieść. Daje to możliwość zastosowania kotew kompozytowych RM nie tylko przy wzmacnianiu/ocieplaniu obiektów wykonanych w systemie W-70 lub Wk-70 ale również przy termomodernizacji innych obiektów wykonanych w ogólnie pojętym systemie wielkiej płyty.
Idea systemu jest prosta. Mianowicie: zastąpienie dotychczasowych systemów wzmacniających TYLKO warstwę fakturową, systemem który wzmacnia warstwę fakturową i dybluje nową izolację termiczną w jednym procesie technologicznym, bez konieczności używania zaawansowanych narzędzi i wysoko wykwalifikowanych pracowników.
Obecnie stosowane systemy wzmacniania warstwy fakturowej w płytach warstwowych to: wklejane w warstwę nośną za pomocą żywic pręty stalowe, stalowe łączniki rozporowe, stalowe konsole podtrzymujące warstwę fakturową oraz pary wklejanych prętów, z czego jeden jest prostopadle skierowany do ściany zewnętrznej a drugi ułożony jest pod pewnym kątem do ściany. Każdy z tych systemów ma jedną zasadniczą wadę: służy tylko do wzmocnienia warstwy fakturowej. Dopiero Po wykonaniu tego wzmocnienia dokonuje się dalszych praz termoizolacyjnych.
Chcąc dobrać jakikolwiek system wzmocnienia warstwy fakturowej projektant musi najpierw oszacować wartości obciążeń wynikających głównie z ciężaru własnego poszczególnych warstw. Zakładając, że będziemy brali pod uwagę jedną z najczęściej stosowanych płyt warstwowych o wymiarach 2,8×4,6m i warstwach zgodnych z rysunkiem:
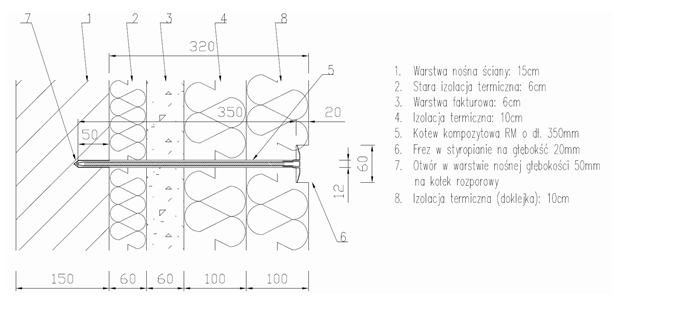
Otrzymujemy:
– obciążenie od ciężaru własnego warstwy fakturowej: A = 12,88m2, t = 0,06m, r = 24kN/m3
– obciążenie od ciężaru starej izolacji termicznej: A = 12,88m2, t = 0,06m, r = 0,3kN/m3
– obciążenie od ciężaru nowej izolacji termicznej: A = 12,88m2, t = 0,15m, r = 0,3kN/m3
Przechodząc na wartość obliczeniową obciążenia otrzymujemy:
Taką wartość oddziaływującej pionowo siły muszą przenieść kotwy wzmacniające.
Na tej podstawie można dobrać kotwy, np.: kotwa chemiczna (spośród dostępnych na rynku) mającą nośność na ścinanie wg producenta:
Stąd: Vd / VRd = 26,12/6,667 = 3,91 szt. – dobrano 4 szt. kotwy chemiczne
Z kolei stosując system kotwy kompozytowej RM otrzymujemy:
Średnia nośność jednej kotwy na ścinanie, w zależności od średnicy pręta kompozytowego wynosi:
Warto zaznaczyć, iż podane wartości średnie nośności na ścinanie pojedynczej kotwy kompozytowej RM korespondują z przemieszczeniem pionowym wynoszącym zaledwie 3,0mm.
Stąd potrzebna ilość kotew w zależności od ich średnicy:
Należy przy tym pamiętać, że wszystkie przyjęte ilości sztuk odnoszą się do całej płyty której pole powierzchni wynosi 12,88m2. Stąd na 1m2 wzmacnianej ściany otrzymujemy:
– przykładowy system kotwa chemiczna (spośród dostępnych na rynku): 4szt. / 12,88m2 = 0,31 szt./m2
– kotwa kompozytowa RM 5,5mm: 38szt. / 12,88m2 = 2,95 szt./m2
– kotwa kompozytowa RM 7,5mm: 22szt. / 12,88m2 = 1,71 szt./m2
Podsumowując powyższe wyliczenia, używając dostępnych na rynku rozwiązań wzmacniających warstwę fakturową otrzymujemy mniejszą ilość kotew, jednakże wzmacniają one TYLKO ową warstwę. Ponadto, kotwy te w sposób mocno punktowy przenoszą obciążenia na część nośną ściany warstwowej. Ich ilość na 1m2 ściany wynosi zaledwie 0,31 szt.
Stosując prototypowy system kotwy kompozytowej RM o średnicy pręta 5,5mm otrzymujemy potrzebne 3 kotwy na 1m2 ściany. Można przyjąć zastosowanie 4 szt./m2 ściany otrzymując tym samym proponowany układ dyblowania i wzmacniania jednocześnie zgodny z rysunkiem (schemat II):
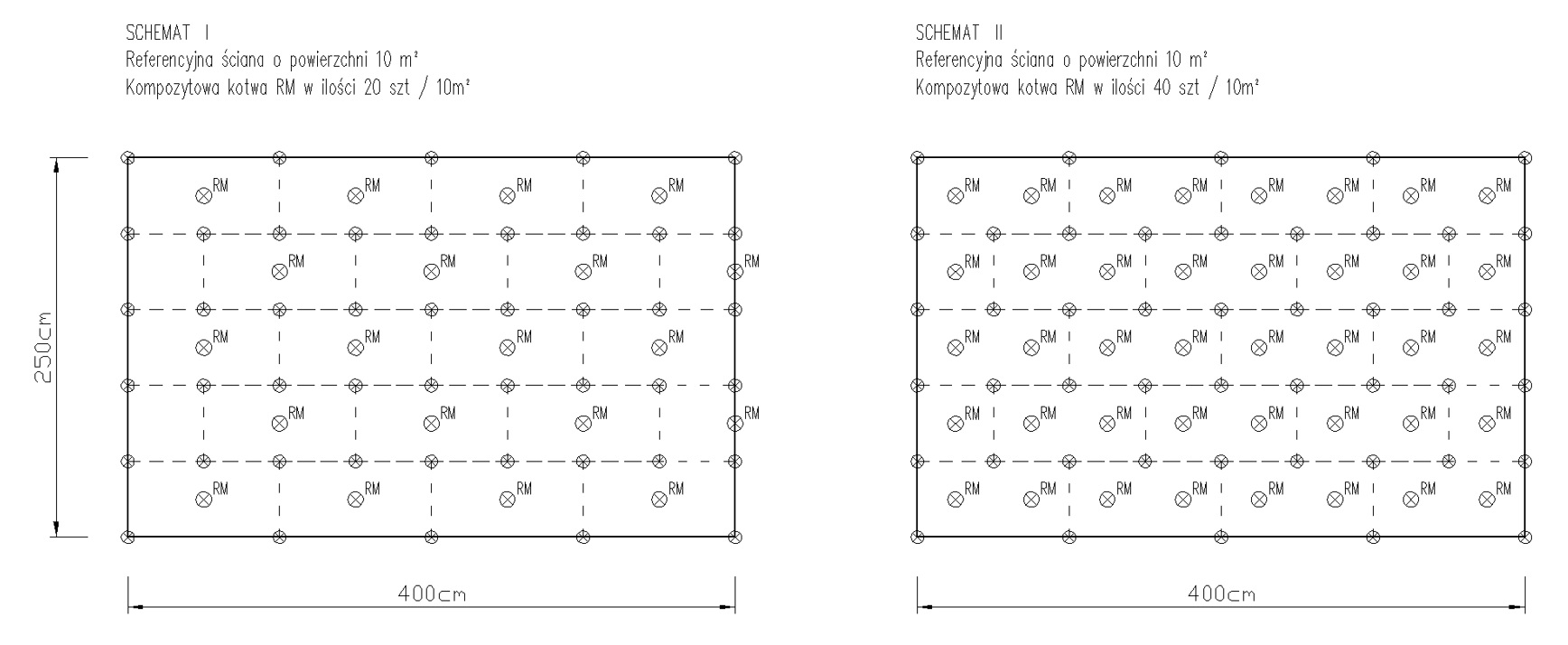
Stosując kotwę kompozytową RM o średnicy pręta 7,5mm otrzymujemy 2 szt./m2 ściany, a to z kolei odpowiada pierwszemu schematowi montażowemu z powyższego rysunku.
Zatem zastosowanie prototypowego systemu dyblo-kotwo-łączników zwanych kotwami kompozytowymi RM eliminuje dwuetapowość procesu termomodernizacji budynków wykonanych z wielkiej płyty. Ujednolica proces prowadzenia pracy termomodernizacyjnych. W jednym cyklu pracy wzmacniamy warstwę fakturową oraz dyblujemy warstwę izolacyjną. Dodatkowo dostajemy niemalże powierzchniowe połączenie warstwy fakturowej z częścią nośną ściany, uzyskując efekt przeszycia.